Description
T91 steel is a new type of martensitic heat-resistant steel developed by American National elephant ridge laboratory and Metallurgical Materials Laboratory of American combustion engineering company. On the basis of 9Cr1MoV steel, it reduces the carbon content, strictly limits the content of sulfur and phosphorus, and adds a small amount of vanadium and niobium for alloying.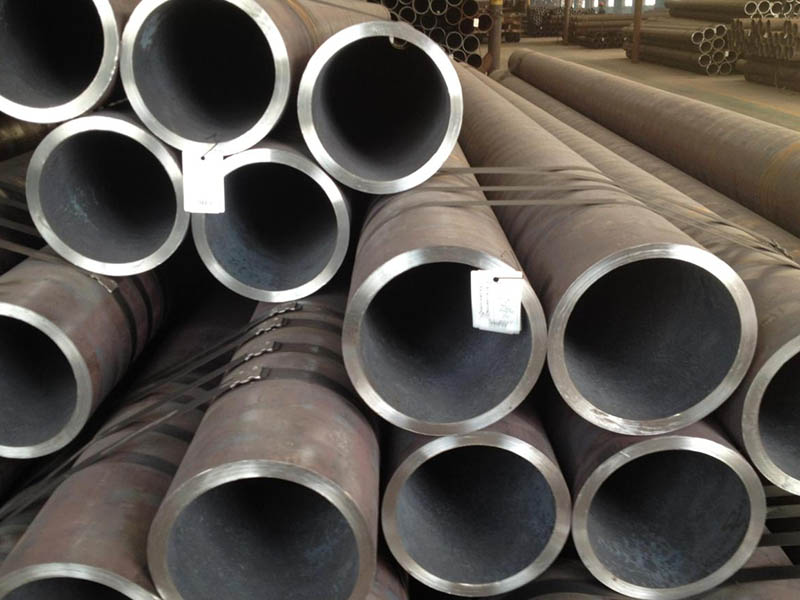
Table 1 chemical composition of T91 Steel%
The final heat treatment of T91 is normalizing + high temperature tempering. The normalizing temperature is 1040 ℃, the holding time is not less than 10 min, the tempering temperature is 730 ~ 780 ℃, and the holding time is not less than 1 h. The microstructure after the final heat treatment is tempered martensite.Mechanical properties
Tensile strength of T91 steel at room temperature ≥ 585 MPa, yield strength at room temperature ≥ 415 MPa, hardness ≤ 250 Hb, elongation (standard circular sample with 50 mm gauge distance) ≥ 20%, allowable stress value [ σ] 650℃=30 MPa.Welding performance
According to the carbon equivalent formula recommended by the international welding society, the carbon equivalent of T91 is It can be seen that T91 has poor weldability. T91 steel has a large tendency of cold crack and is prone to delayed crack under certain conditions. Therefore, the welded joint must be tempered within 24 hours after welding. The microstructure of T91 after welding is plate and strip martensite, which can be changed into tempered martensite after tempering, and its properties are superior to plate and strip martensite. When the tempering temperature is low, the tempering effect is not obvious, and the weld metal is easy to age and embrittlement; If the tempering temperature is too high (exceeding AC1 line), the joint may be austenitized again and hardened again in the subsequent cooling process. At the same time, as mentioned earlier in this paper, the influence of joint softening layer should be considered in the determination of tempering temperature. Generally speaking, the tempering temperature of T91 is 730 ~ 780 ℃. The tempering constant temperature time of T91 after welding shall not be less than 1 h, so as to ensure the complete transformation of its structure into tempered martensite. In order to reduce the residual stress of T91 steel welded joint, the cooling rate must be controlled less than 5 ℃ / min. The welding process of T91 steel can be shown in Figure 3. Preheat 200 ~ 250 ℃; ② Welding, interlayer temperature 200 ~ 300 ℃; ③ Cooling after welding, with the speed of 80 ~ 100 ℃ / h; ④ 100 ~ 150 ℃ for 1 h; ⑤ Tempering at 730 ~ 780 ℃ for 1 h; ⑥ Cool at a rate not greater than 5 ℃ / min. T91 Steel relies on the principle of alloying, especially adding a small amount of trace elements such as niobium and vanadium. Its high temperature strength and oxidation resistance are greatly improved compared with 12 cr1mov steel, but its welding performance is poor. The pin test shows that T91 steel has a large tendency of cold crack. Selecting preheating 200 ~ 250 ℃ and interlayer temperature 200 ~ 300 ℃ can effectively prevent cold crack. T91 must be cooled to 100 ~ 150 ℃ for 1 h before post weld heat treatment; Tempering temperature 730 ~ 780 ℃, holding time not less than 1 h. The above welding process has been applied to the manufacturing and production practice of 200 MW and 300 MW boilers, with satisfactory results and great economic benefits.The steel grade of T91 seamless steel pipe corresponding to T91 steel is x10crmovnnb91 in Germany, hcm95 in Japan and tuz10cdvnb0901 in France.Heat treatment process