Description
45# seamless steel pipe after quenching and tempering treatment has good comprehensive mechanical properties and is widely used in various important structural parts, especially those connecting rods, bolts, gears and shafts working under alternating load. However, the surface hardness is low and not wear-resistant. Quenching and tempering + surface quenching can be used to improve the surface hardness of parts.Recommended heat treatment temperature: normalizing 850, quenching 840, tempering 600. 45 steel is a high-quality carbon structural steel with low hardness and easy cutting. It is often used as formwork, shoot, guide post, etc. in the mold, but it must be heat treated. 1. 45 steel is qualified if its hardness is greater than HRC55 (up to HRC62) after quenching and before tempering. The highest hardness for practical application is HRC55 (high frequency quenching hrc58). 2. The heat treatment process of carburizing and quenching shall not be adopted for 45 steel. The quenched and tempered parts have good comprehensive mechanical properties and are widely used in various important structural parts, especially those connecting rods, bolts, gears and shafts working under alternating load. However, the surface hardness is low and not wear-resistant. Quenching and tempering + surface quenching can be used to improve the surface hardness of parts. Carburizing treatment is generally used for heavy-duty parts with wear-resistant surface and impact resistant core, and its wear resistance is higher than quenching and tempering + surface quenching. The surface carbon content is 0.8-1.2%, and the core is generally 0.1-0.25% (0.35% in special cases). After heat treatment, the surface can obtain high hardness (HRC58-62), low core hardness and impact resistance. If 45 steel is carburized, hard and brittle martensite will appear in the core after quenching, which will lose the advantage of carburizing treatment. The carbon content of materials with carburizing process is not high, and the core strength can reach very high at 0.30%, which is rare in application. 0.35% have never seen examples, which are only introduced in textbooks. The process of quenching and tempering + high frequency surface quenching can be adopted, and the wear resistance is slightly worse than carburizing. The recommended heat treatment system for 45 steel specified in GB / t699-1999 is 850 ℃ normalizing, 840 ℃ quenching and 600 ℃ tempering, and the yield strength is ≥ 355MPa. According to GB / t699-1999, the tensile strength of 45 steel is 600MPa, the yield strength is 355MPa, the elongation is 16%, the reduction of area is 40%, and the impact energy is 39j. 1、 Functions, structural features and technical requirements of shaft parts Shaft parts are one of the typical parts often encountered in machines. It is mainly used to support transmission parts, transmit torque and bear load. Shaft parts are rotating parts, whose length is greater than the diameter. They are generally composed of outer cylindrical surface, conical surface, inner hole, thread and corresponding end face of concentric shaft. According to different structural shapes, shaft parts can be divided into optical axis, stepped axis, hollow axis and crankshaft. The shaft with an aspect ratio less than 5 is called a short shaft, and the shaft with an aspect ratio greater than 20 is called a slender shaft. Most shafts are between the two. The shaft is supported by a bearing, and the shaft section matched with the bearing is called a journal. The journal is the assembly benchmark of the shaft, and its accuracy and surface quality are generally required to be high. Its technical requirements are generally formulated according to the main functions and working conditions of the shaft, usually including the following items: 1. In order to determine the position of the shaft, the journal with supporting function of dimensional accuracy usually requires high dimensional accuracy (it5 ~ it7). Generally, the dimensional accuracy of shaft journal for assembling transmission parts is low (IT6 ~ it9). 2. Geometric accuracy the geometric accuracy of shaft parts mainly refers to the roundness and cylindricity of journal, outer cone, Morse taper hole, etc. generally, its tolerance shall be limited to the dimensional tolerance. For inner and outer circular surfaces with high accuracy requirements, the allowable deviation shall be marked on the drawing. 3. Mutual position accuracy the position accuracy requirements of shaft parts are mainly determined by the position and function of the shaft in the machine. Generally, the coaxiality requirements of the Journal of the assembled transmission parts on the supporting journal shall be ensured, otherwise the transmission accuracy of the transmission parts (gears, etc.) will be affected and noise will be generated. For ordinary precision shafts, the radial runout of the mating shaft section to the supporting journal is generally 0.01 ~ 0.03mm, and for high-precision shafts (such as main shafts), it is usually 0.001 ~ 0.005mm. 4. The surface roughness of the shaft diameter matched with the transmission parts is generally ra2.5 ~ 0.63 μ m. The surface roughness of the supporting shaft diameter matched with the bearing is Ra0.63 ~ 0.16 μ m。Blanks and materials of shaft parts
1. Blanks of shaft parts. According to the use requirements, production type, equipment conditions and structure, blank forms such as bars and forgings can be selected for shaft parts. For the shaft with little difference in outer circle diameter, it is generally dominated by bar; For stepped shafts or important shafts with large difference in outer circle diameter, forgings are often selected, which not only saves materials, reduces the workload of machining, but also improves mechanical properties. According to the different production scale, the forging methods of blank include free forging and die forging. Free forging is often used in small and medium-sized batch production, and die forging is used in mass production. 2. Materials of shaft parts shaft parts shall select different materials according to different working conditions and use requirements and adopt different heat treatment specifications (such as quenching and tempering, normalizing, quenching, etc.) to obtain certain strength, toughness and wear resistance. 45 steel is a common material for shaft parts. It is cheap. After quenching and tempering (or normalizing), it can obtain better cutting performance, high strength and toughness and other comprehensive mechanical properties. The surface hardness after quenching can reach 45 ~ 52hrc. 40Cr and other alloy structural steels are suitable for shaft parts with medium precision and high speed. After quenching, tempering and quenching, this kind of steel has good comprehensive mechanical properties. Bearing steel GCr15 and spring steel 65Mn, after quenching and tempering and surface high-frequency quenching, the surface hardness can reach 50 ~ 58hrc, and have high fatigue resistance and good wear resistance. They can manufacture high-precision shafts. 38crmoaia nitrided steel can be selected for the spindle of precision machine tools (such as grinder sand axle and coordinate boring machine spindle). After quenching and tempering and surface nitriding, this steel can not only obtain high surface hardness, but also maintain a soft core, so it has good impact toughness. Compared with carburized quenched steel, it has the characteristics of small heat treatment deformation and higher hardness. 45 steel is widely used in mechanical manufacturing. This steel has good mechanical properties. However, this is a medium carbon steel with poor quenching performance. No. 45 steel can be hardened to hrc42 ~ 46. Therefore, if the surface hardness is required and the superior mechanical properties of 45# steel are expected to be brought into play, the surface of 45# steel is often carburized and quenched, so that the required surface hardness can be obtained.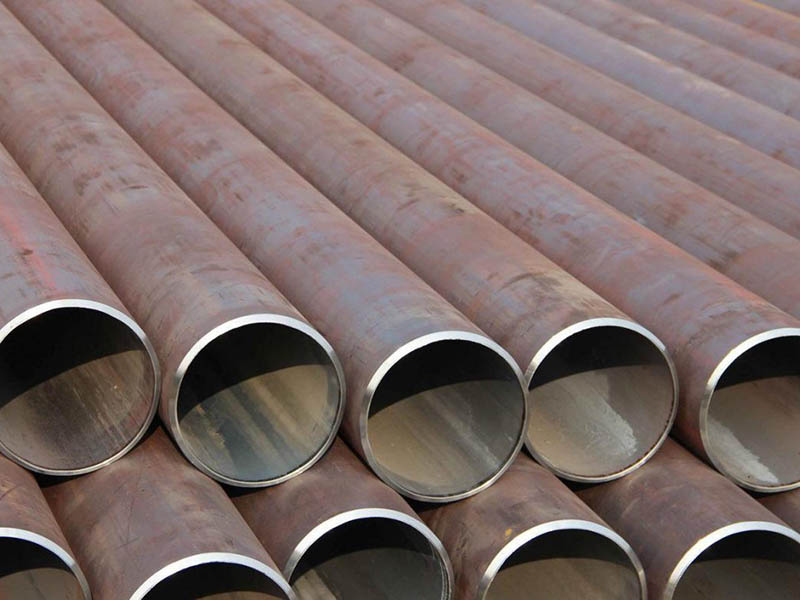